The car manufacturer relies on 5mw laser pointer welded blank (LWB) to control or reduce the amount of material used in various parts of the vehicle, such as the frame and body. LWB is composed of sheet metal with different thickness and grade. These welding plates must meet the requirements of vehicle collision safety while satisfying other relevant regulations. Using the numerical simulation to optimize the LWB welding process, by looking for the optimal combination of the two grades of welded steel grades, the solder plates produced by them can ensure excellent performance and minimize the weight of the parts.
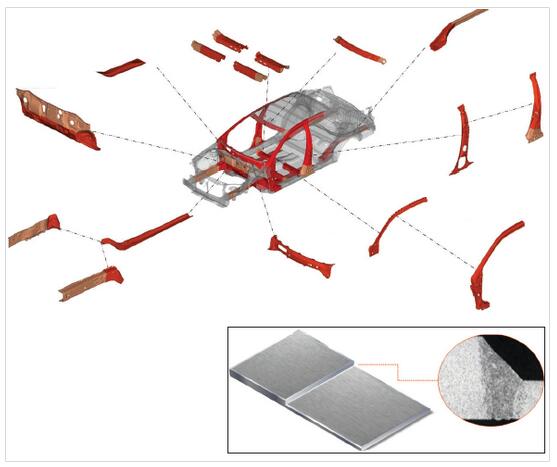
The use of advanced high-strength pressure hardening steel, the installation of the steel plate was optimized, so that the specific area of the car to maintain the strength of the performance at the same time more thin. Ultimately, it is desirable to achieve excellent welding quality to ensure that the welding meets the safety requirements of the crash test. A safe welding can not be broken or broken during the test, otherwise the weldment will not pass the safety test. The use of high power laser pointer welding of concentrated heat source will be converted into molten metal molten steel, used to form a narrow and deep weld.
High-power lasers can produce large amounts of energy, causing some metal to evaporate. In the process of melting, the density of the steel will decrease rapidly and the volume will increase accordingly, and the movement of the material will increase, resulting in high pressure steam. At this time will produce a 'keyhole', it is the 20mw laser pointer impact point on a narrow hole. The steel around the hole melts to form a pool. After the liquid steel cools, it will connect two sheets of sheet metal. The fundamental cause of most mechanical failures is the presence of defects in the weld, since the weld points are connected to different materials. If the connection is improperly handled, it will eventually cause the stress to be too large. "Improper welding parameters may also cause instability of the welding point, resulting in welds in the pores, part of the penetration or undercut, resulting in the connection is not strong.
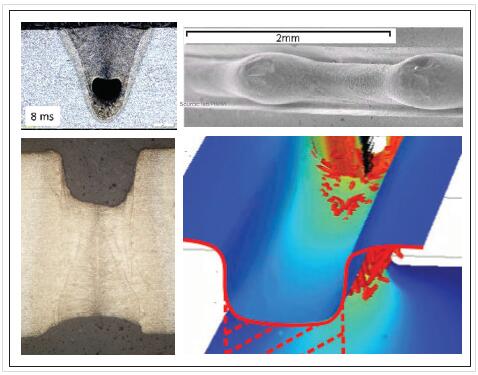
Among the factors that affect the quality of welding, burning laser pointer power, material reflection of the laser beam, welding speed and wavelength and other details of the keyhole around the heat transfer, phase change and fluid flow have an impact. In particular, due to the presence of phase change and thermal load, the keyhole angle and the shape of the molten pool will have a greater impact on the fluid flow characteristics. High quality welding requires full penetration of the steel plate. When the energy density is limited, the power is too low or the welding speed is fast, local penetration will occur. Partial penetration can cause material to undercut, and eventually leave a gap between the two plates.
To provide customers with the right 10mw laser pointer tailor-welded blanket, you need to choose the correct combination of welding parameters. By adjusting the grade and thickness of the steel plate in order to meet the customer to meet the vehicle crash test specifications, weight requirements and cost requirements of the laser tailor welded blanks. A series of process conditions are determined by simulation to ensure that defective welds are produced. Knowing the physical phenomena of these interactions and coupling them together for simulation, rather than doing multiple studies in parallel, gives us a great deal of convenience. Has been committed to helping the automotive industry to reduce the weight of the body and to ensure that the welding products have excellent quality, so as to protect the driver in the safety of driving a car.